Sequence of operation, at least in general;
1) Launch the MasterCam application and open the inventor file. Remember dont import the file.
2) Add square tab on the contours so that it wouldn't break your mill bits.
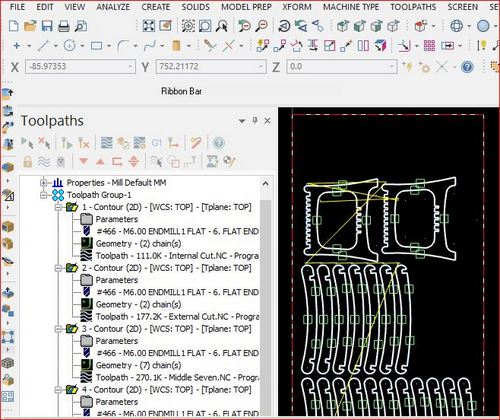
MasterCam Work Page
3) Select Machine Type - Mill (Default)
4) Select Toolpath - Contours
5) Start Chaining the lines in MasterCam
6) Ensure the Clearance, Retract, Feed Plane, Top of Stock and Depth have their Absolute ticked or checked. Very Imporant !!!
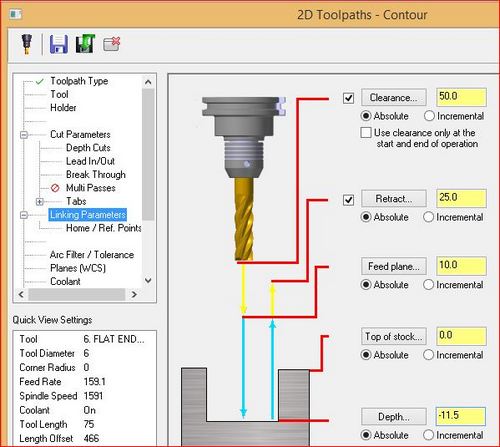
MasterCam Linking Parameter Page
7) Click G1 to generate gcode in MasterCam Code Expert and saved the file as xxx.NC into your flash drive
8) Next launch JG application to convert your xxx.NC into xxx.JG
The reason for this seemingly illogical step is because this Router only understand "Japanese" and knows no other languages whether in writing or speech.
9) Now prepare your plywood stock onto the router and clamped it down properly
10) Set the router XYZ to the workpiece zero position.